How IoT Solutions Can Improve BusinessHow IoT Solutions Can Improve Business
The Internet of Things can drive improved business outcomes for industrial applications.
April 12, 2017
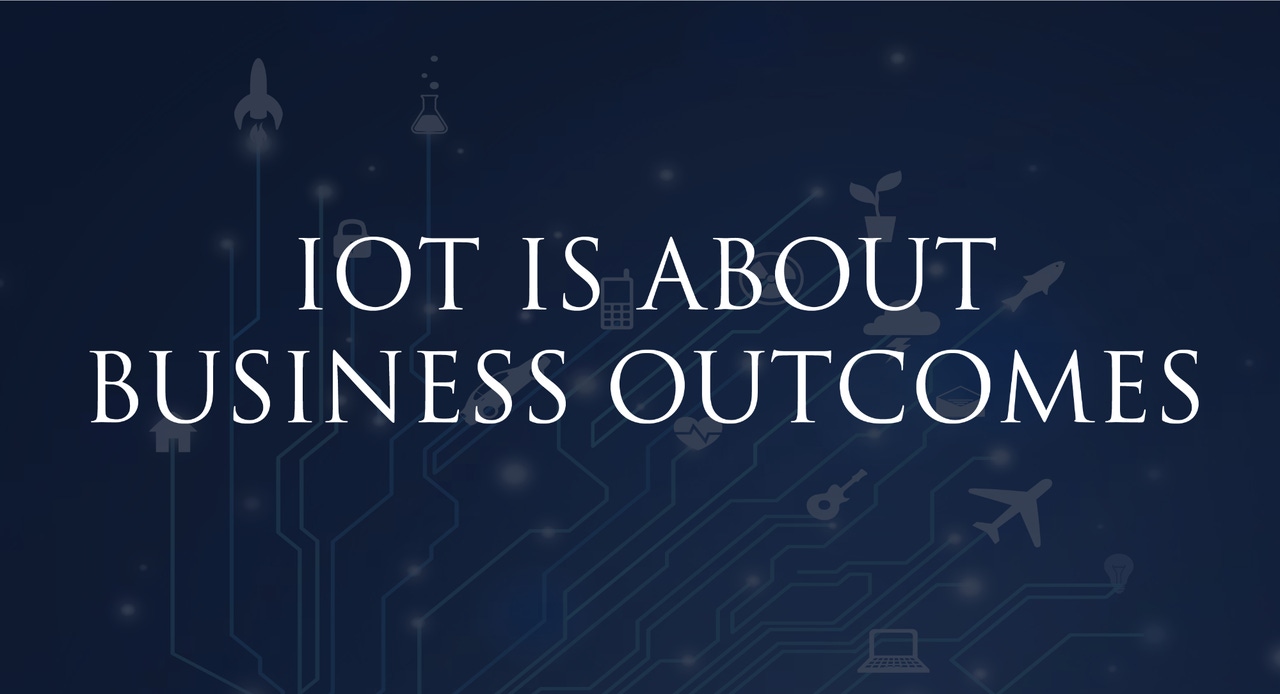
By Vince Vasquez
When we think of IoT (Internet of Things), we tend to think about consumer products and services, such as Fitbit and home automation. While many might question why a coffee pot needs to communicate with a toaster, at a macro level there is a clear opportunity for precision technology—used in IoT solutions and deployed by businesses—to dramatically transform the planet’s fundamental infrastructure. At more of a micro level, there is a measurable opportunity for precision technology to improve business outcomes for both builders and buyers of precision products and services.
This article is written for those considering building or buying precision technologies used in IoT solutions and who are interested in understanding better, potentially achievable, improved business outcomes.
This article uses content from the book Precision IoT by Timothy Chou. If you’d like to venture deeper into this topic and better understand the fundamentals of IoT, consider taking the free Fundamentals of IoT online course based on Precision IoT and offered by the IoT Institute.
Improved Business Outcomes for Builders of Precision Machines
We’ll start by exploring the available enhanced business outcomes for those who manufacture machines with regards to improved quality of service, reduced cost of service, and improved machine design. We’ll also look at potential new business models available to manufacturers in a world with deployed precision technology.
Improved Quality of Service
In the computing industry, both hardware and software companies have traditionally provided maintenance services. In the case of software, this is typically priced as a percentage of the purchase price; this business model generated the most revenue and profit for the first generation of enterprise software companies such as Oracle.
Of course, the manufacturers of machines can do the same. By connecting their Things to the Internet, builders can provide better service for their machines—better availability, security, performance, and change management.
Better availability means less downtime for the customer; better security means ensuring there aren’t any viruses and notifying customers when security patches are available; better performance means telling the customer how to better use the machine; and better change management means ensuring the customer knows there are new features available with a simple software upgrade.
In addition, based on usage data, equipment suppliers can suggest more appropriate models or companion equipment. We’ve seen Amazon provide personal and relevant information regarding products that we might be interested in, so why not do the same on the industrial side?
Reduced Cost of Service
Traditional computer hardware service requires “rolling a truck” to bring spare parts to repair or service a machine. By connecting the machines, not only could you remotely diagnose problems, but also ensure that you bring the right part.
Maintenance of machines is often left as a cost to the buyer and these costs can be significant. One large construction rental company spends more than $1 billion per year on maintenance. General practice today is to implement time-based maintenance. While this is the best we can do in a non-connected world, once we can connect more Things, it becomes possible to know the difference between a forklift that’s been used in a sandy, humid, hot environment and one that’s been in an air-conditioned warehouse. Knowing precisely when machines need service and doing it proactively has significant operational and economic benefit.
Improved Machine Design
Businesses can also gain valuable information from data streaming from their machines out in the field in order to make product enhancements.
For example, Arrow Electronics spearheaded an effort to create an IoT-enabled race car for Sam Schmidt, a former race car driver who became a paraplegic after a racing accident. Given Sam had lost the use of his arms and legs, this race car was designed to enable him to accelerate and brake using air pressure through a mouthpiece, and steer with subtle head movements tracked in real time via sensors on his helmet. Additional sensors pull the car’s performance data, in-vehicle environment data, and driver data such as heart rate and body temperature.
All of this and more is captured and forwarded to the cloud for analysis so continuous improvements can be made to the car. As a testimony to the project’s success, in 2016, Sam achieved 152 mph during practice laps at the Indianapolis 500 and completed the Broadmoor Pikes Peak International Hill Climb in Colorado, managing to reach 80 mph on some straightaways.
New Business Models
Manufacturers have traditionally focused on producing a physical good and capturing value by transferring ownership of that good to the customer; the owner is then responsible for service and usage costs while assuming the risks of downtime, product failures, and defects not covered by warranties. Smart, connected products allow the radical alteration of this long-standing business model.
Luckily, we can learn from our friends in the software product industry. Early on we created products and sold them on a CD; if you wanted the next product, you’d have to buy the next CD. As software products became more complex, companies like Oracle moved to a business model where you bought a product license and a support and maintenance contract. Over time, this became the largest and most profitable component of many enterprise software product companies.
Next, these companies said if you connect your machines they could offer you advisory services. As the manufacturer of the software with knowledge of how it was being used, you could tell the client exactly how to increase security or performance. Of course, once you can tell the customer how to fully manage the software, it’s a simple step to offer to do it for them.
The second generation of enterprise software companies (WebEx, Salesforce, etc.) built software and processes so they could manage the security, availability, performance, and change themselves, guaranteeing service and support levels. These business models allowed for customers to purchase the services on demand and resulted in differentiated and highly valued software-as-a-service companies.
Hardware product companies can now leverage this idea—whether it’s for a wind turbine or CT scanner—by adding three new business models.
Service and Support Contracts. Machine sales bundled with warranty or service contracts. Service contracts allow the manufacturer to keep service in-house and capture more of the value from service efficiencies.
Assisted Services. Connect to the machine and offer advice to improve the availability, security, or performance of the machine.
Machine-as-a-Service. The machine manufacturer retains ownership and takes full responsibility for the security, availability, performance, and change of the product for a recurring charge.
The Internet has enabled the “as-a-service” business model for IT infrastructure and software. IoT enables “machines-as-a-service” business models for all kinds of other products, potentially allowing companies to shift from selling products to selling services based on those products; this model can transform large capital expenditures into a pay-by-usage operating expense. Examples of this trend are proliferating—power by the hour, air by the minute, or cubic meters of coal mined.
Improved Business Outcomes for Buyers of Precision Machines
Next, we explore potential benefits achieved by those who buy precision technologies and deploy IoT solutions in terms of lower consumables costs, preemptive maintenance, higher quality product or service, and improved health and safety.
Lower Consumables Costs
Many machines consume materials during operations, like fuel in an airplane or ink in a high-speed printer. These consumables often form a large portion of the operational cost structure. For instance, in the airline industry, the single largest operational cost is fuel—in some cases that’s nearly 30% of the total cost of the flight.
In the railroad business, New York Air Brake has engineered a product called LEADER to help operate trains more precisely, which is being used by Norfolk Southern Railway, which operates over 22,000 route miles in 22 eastern states. They attribute a 5% fuel savings to its deployment, resulting in not only 10.8 million gallons of diesel fuel saved per year, but also the avoidance of more than 109,500 metric tons of greenhouse gas emissions.
Preemptive Maintenance
IoT-enabled monitoring systems can notify company personnel when maintenance needs to occur before systems break or worse.
For example, consider the challenge faced by distribution facilities deploying large racking systems in their warehouses. Operated equipment, such as forklifts, can degrade the structural integrity of the racks through many low-energy impacts. Over time, the often-bumped racking units may fail and collapse altogether, causing a catastrophe in the warehouse and potentially putting the facility completely out of action.
A-Safe builds an IoT-enabled safety system called RackEye that provides continuous monitoring of racking structures, with sensors that detect damage to the racking units. This data is communicated in real time to the Autodesk Fusion Connect IoT platform, which then sends notifications to appropriate personnel when a rack has been bumped and its structural integrity is at risk.
Higher Quality Product or Service
Connecting machines to the network and collecting the data produced can enable businesses to learn and improve the precision of operations. For example, consider equipment rental used in precision construction.
United Rental offers thousands of classes of equipment to construction and industrial companies, manufacturers, utilities, and municipalities decided to connect its rented equipment. By doing so, the company can keep track of the exact location of its equipment. A mobile app enables managers to see where the driver dropped it off and where it’s being used.
An additional benefit is the ability to bill for fractions of days based on the equipment’s use record. In a non-connected state, the industry standard is to charge for equipment in eight-hour-per-day increments. The result can be a very large bill at the end of the rental. In a connected state, the company knows precise usage in real time and can bill accordingly.
Improved Health
SensiumVitals is a wireless system designed to monitor the vital signs of patients in all areas of a hospital setting where patients would not normally be continuously monitored. The product is a light-weight, wearable, wireless, single-use patch that takes vital signs and wirelessly communicates that data to clinicians via the hospital’s IT infrastructure.
This patch provides continuous monitoring of heart rate, respiration rate, and temperature. The system takes patient measurements every two minutes, which is significantly more often than current manual practices where the majority of patients have vital signs taken only once every 4–8 hours. Infrequent monitoring can mean that deterioration in patient conditions may go unnoticed, potentially leading to longer hospital stays, more expensive treatments or even admittance to intensive care.
By using three years of historic sensor data derived from the SensiumVitals system, coupled with Code Blue and rapid response events, a team at UC Irvine Medical built a model to predict potential Code Blue events before they happen.
At present, the result of UC Irvine’s work is an ability to predict a Code Blue with reasonable accuracy within 90 seconds of the event, with the goal of being able to make a prediction ten minutes into the future.
Improved Safety
The derailment of an Amtrak train in Philadelphia in 2015 left at least six people dead and created chaos on the heavily traveled Northeast corridor the next morning. We already talked about how New York Air Brake’s assisted services are reducing fuel consumption at Norfolk Southern Railway; this is implemented by providing advice to the train operators on how to operate the train more efficiently. But if you can tell the train operator what to do, it’s a short step to simply having the computers do it.
In fact, by 2018 an automated train is scheduled to go online, running from the north of Australia to Perth to deliver iron ore. Not only will it reduce costs, as the railroad spends $300,000 in salary for these operators, but it will also reduce human error, resulting in a safer railroad.
Summary
While technology is cool, its real use has been to transform businesses. We’re all familiar with the examples from the consumer space (Google, Uber, eBay), but IoT technology has the potential to do the same for builders and buyers of the machines used across industries. For a manufacturer of Things, technology can not only reduce the cost and improve the quality of service, but also deliver new revenue sources. As a business consuming this next generation of Things, you have the ability to use precision machines to deliver higher quality and lower cost food, power and water, and safer and lower cost transportation and healthcare.
If you want to go deeper in this topic, I encourage you to take the free Fundamentals of IoT course offered by the IoT Institute based on the book Precision IoT by Timothy Chou.
You May Also Like